His craft is under threat, and the material he works with is becoming more and more elusive. Christian Calas is looking forward to retirement, and would like to pass on his know-how. Industry’s biggest names are getting involved.
Emmanuel Alder / JSH Magazine & TàG Press +41’s indépendant columnist
Write to him | Insta SWP | Insta JSH® | Facebook | Twitter | Linkedin
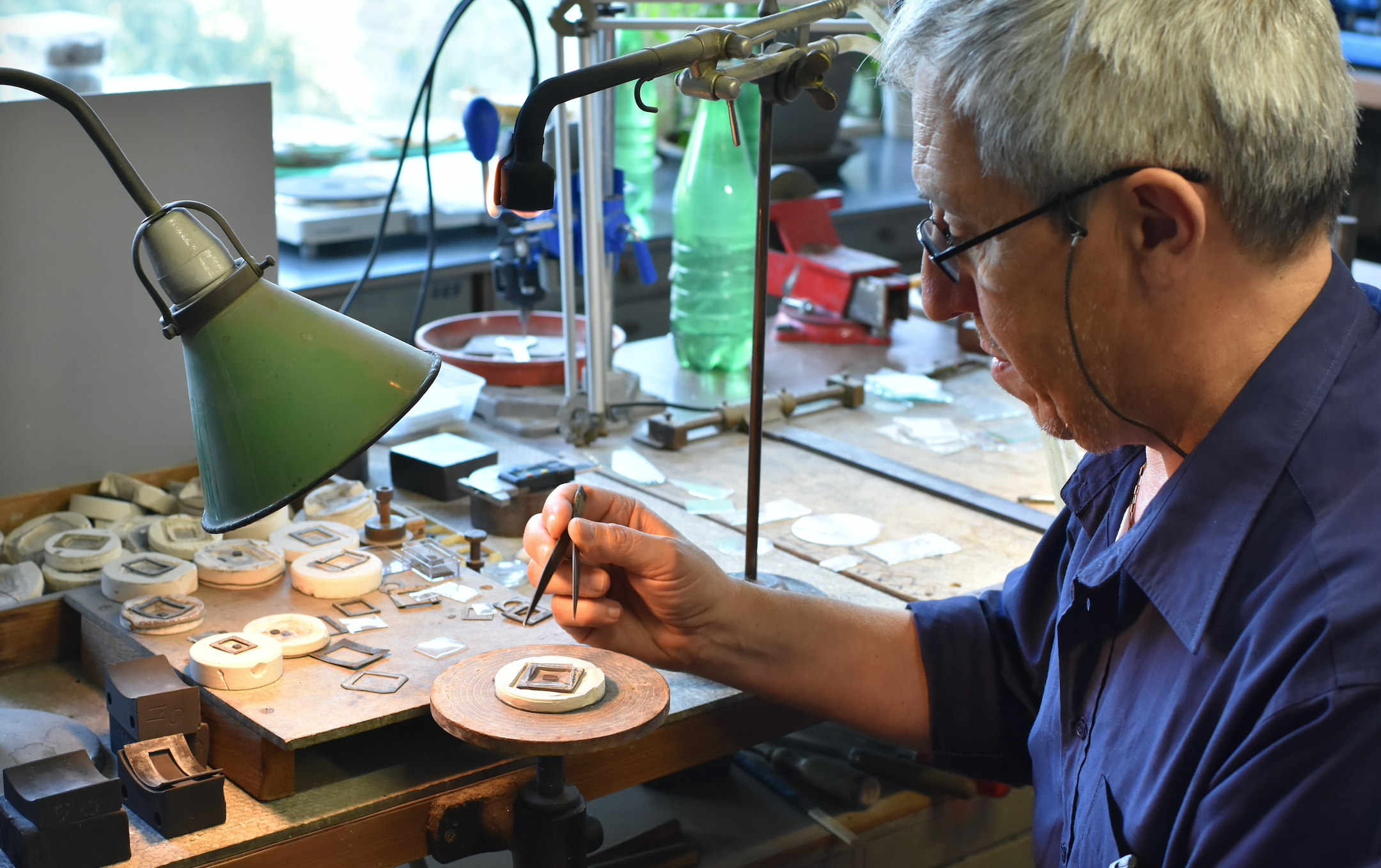
Museum authorities and the most prestigious brands are on the alert. Collectors and auction houses too. Christian Calas is the only one, the last, to master the secrets of mineral glass
A piece of Swiss history
If timepieces have moved on to scratch-resistant sapphire crystal, after the parenthesis of Plexiglas, the mineral glass craftsmanship of the early 20th century, namely the white glass, has no right to disappear. Because who will be able to restore a historic piece, or replace a damaged, broken or lost glass?
The history of watch glass is closely linked to the successes and crises of the entire watchmaking industry. This inevitably eventful history is linked to the name of Tony Vaurillon, who bought “Les Moulins David” in 1898. The company had already been making watch glasses since 1855 along the Quai du Seujet in Geneva. As the watchmaking industry evolved, he gradually transformed what had been a craft workshop into a full-fledged industry. His son took over the business after his death, turning it into a Société Anonyme in 1931.
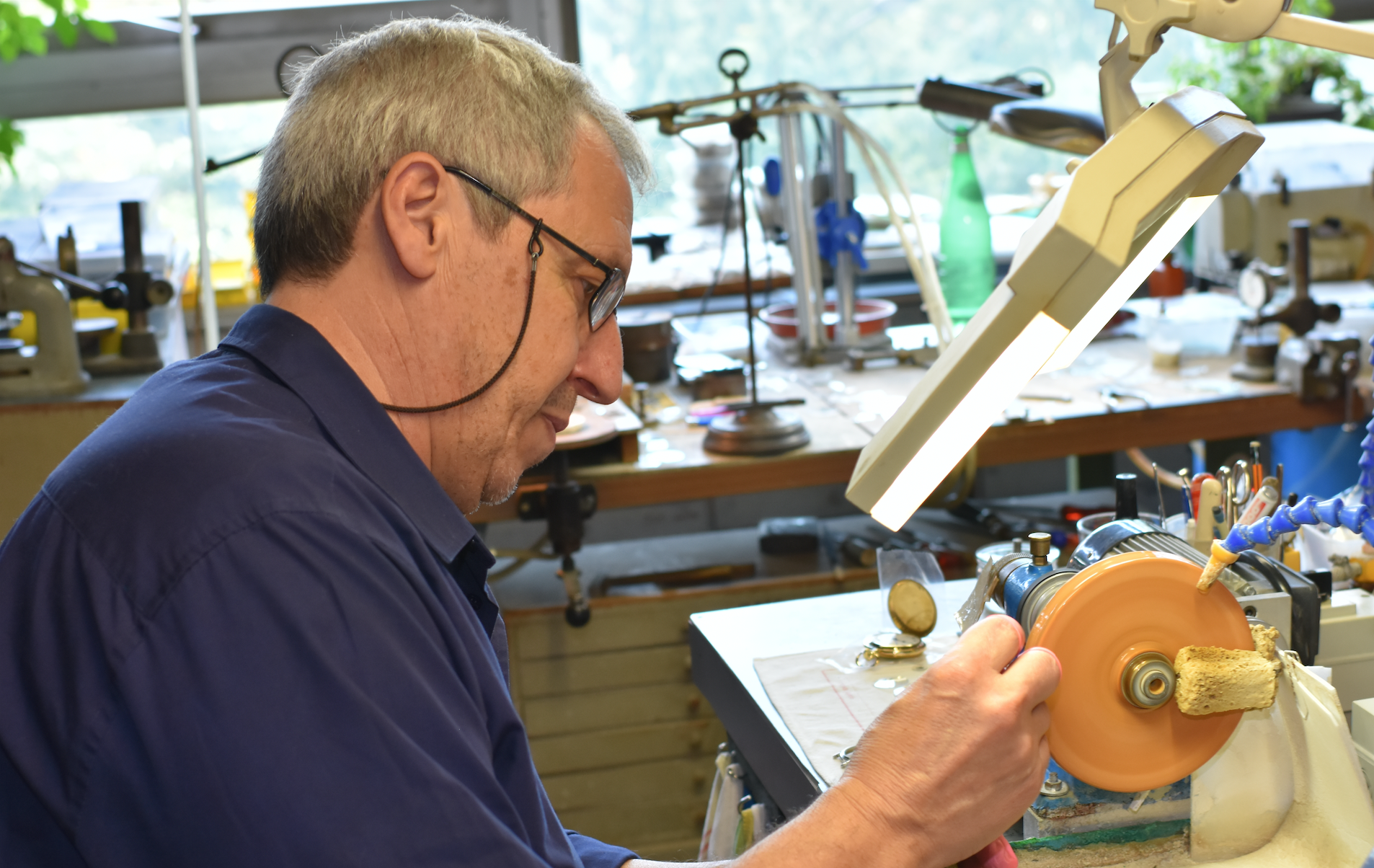
The trade-in
In the mid-70s, the arrival of new production technologies, competition and the downturn in the watchmaking industry sounded the death knell for the company. The “Vaurillon” name was saved by an ex-employee who bought back part of the production equipment and glass stocks. For 25 years, right up to 2006, he continued to operate under the name “Atelier Vaurillon“. He then passed the flame of this now confidential craftsmanship to Christian Calas, a cook from south-west France, who saw in it the opportunity for a career change and independence..
The newcomer spent over a year training and turned his workshop in Geneva’s Rue des Maraîchers into a cross between an Ali-Baba cavern and an alchemist’s lair! A space filled with human warmth and fascinating anecdotes. Christian Calas proudly and passionately narrates these extraordinary pieces temporarily orphaned from their glass. His sunny accent describes his furnaces and the various grinding wheels he uses to reshape broken glass and rectify damaged pieces. While he readily displays his blowtorch (photo), he is more cautious about his famous “glass-bending hammer“.
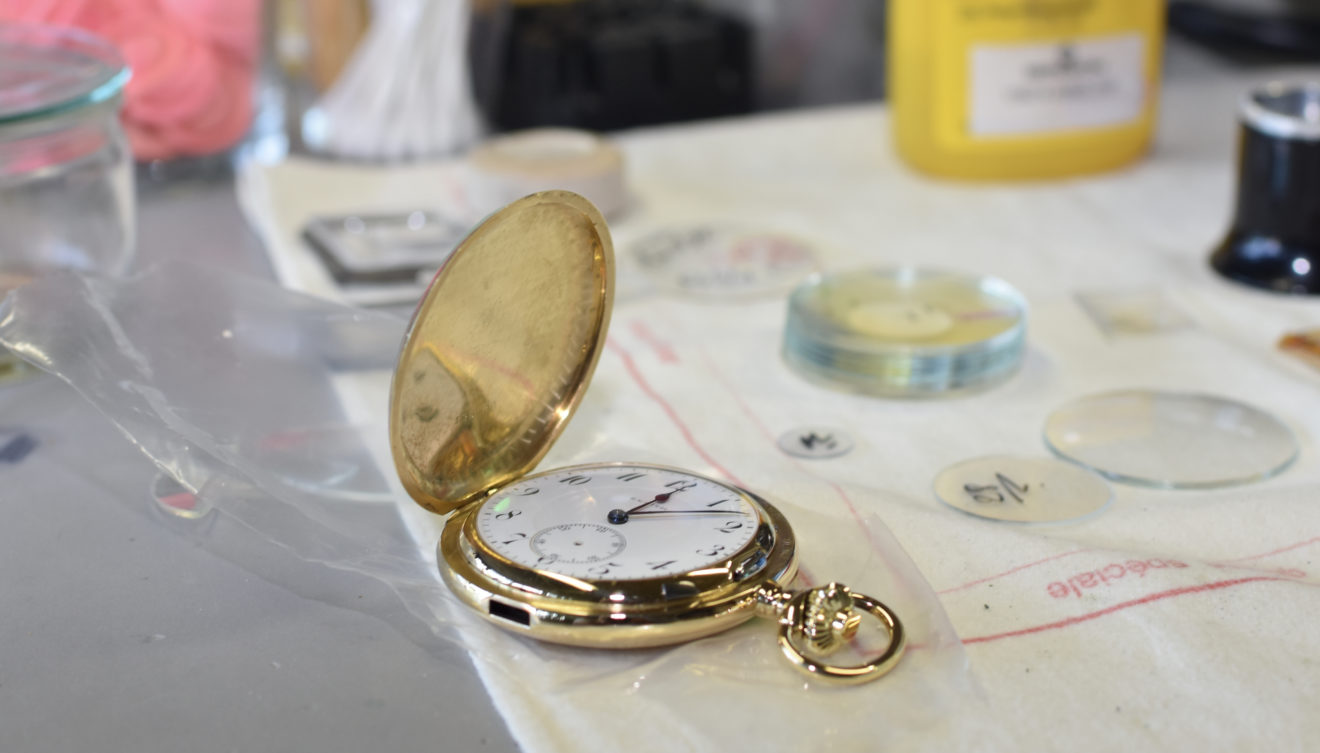
Conservation operation
Today, Christian Calas is Switzerland’s last remaining craftsman capable of producing virtually any custom-made watch glass that private collections or the after-sales departments of major watch manufacturers might require. Although he can also produce Plexiglas or sapphire glass, his expertise and demand are focused on mineral glass, from the tiniest to wall clocks.
Being the only repository of such an expertise is not without a sense of personal accountability. For this heritage is essential to the conservation and repair of priceless objects. At the age of 61, Christian Calas knows only too well that this kind of legacy also benefits the great names in watchmaking who are Atelier Vaurillon’s loyal customers. Without him, they would find themselves definitively totally deprived of any other alternative.
A project is therefore under examination: to provide financial backing, as a form of patronage, both for the year and a half needed to train a new owner, and for the financial sustainability of the workshop, which would keep its absolute independence from the brand(s) involved. A roadmap that also includes financing the training of several people to limit the risk and prevent any loss of this essential know-how.
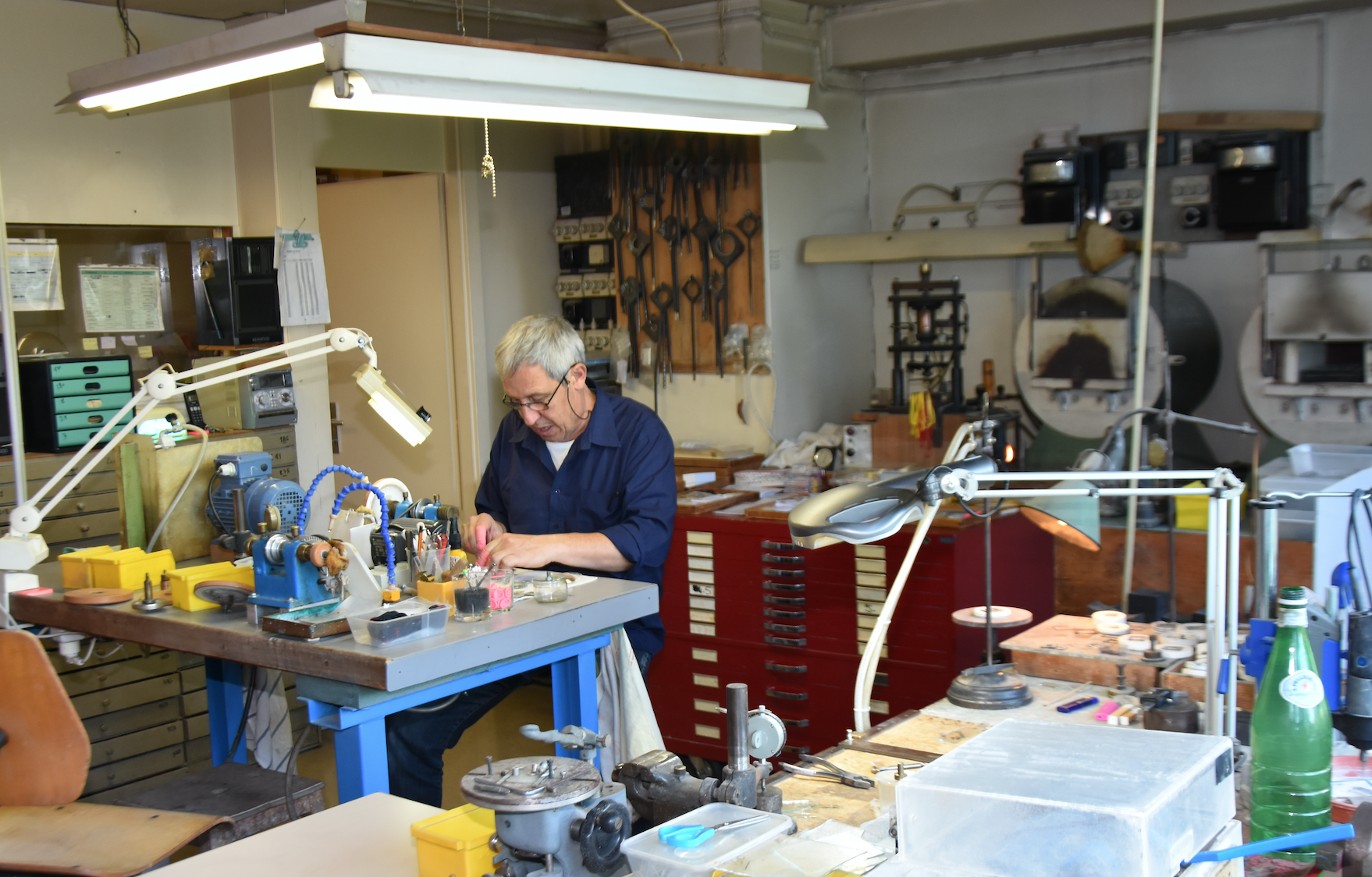
Delightful little secrets
The often stratospheric value of the pieces to be restored, as well as their frailty, often make watchmakers nervous. They hesitate to bring them to his workshop. So, in this case, it’s an empty watchcase, or even a simple carrure or bezel, that are sent to him, perhaps with the reference of the glass to be changed and often accompanied by the broken glass to be replaced. However, most of the time, this is not enough. As happened during my visit, when a very valuable and mechanically delicate pocket watch was lying on his workbench. At first, his customer only wanted a few copies of the missing glass to be sent from his stock of supplies. Then, after two shipments and a few more broken glasses, the complete timepiece ended up in the workshop. Only the experienced craftsman was able to fit the new glass to perfection, as the infinitesimal space between the glass and the hands required his unique expertise.
On another occasion, two watches belonging to Enzo Ferrari turned up right at the appointed hour and minute, with the owner and an impressive group of security guards in tow. Because the two times 1 million Swiss francs far exceeded his insurance coverage. They left the same day with their new glasses.